Time to read: 7 min
CNC (Computer Numerical Control) machining has been around for decades. CNC machining is more popular than ever with today’s technological advancements in machining, along with a vast array of superior metal alloys such as superalloys. There is a wide array of CNC machining providers from in-house machining services to outsourced manufacturers to the innovative on-demand CNC machining ecosystems. CNC machining is flexible in the fact that it can be utilized for everything from hobby applications to prototype machining to even large-scale, high-volume production. It offers high precision, with little manual labor and excellent quality.
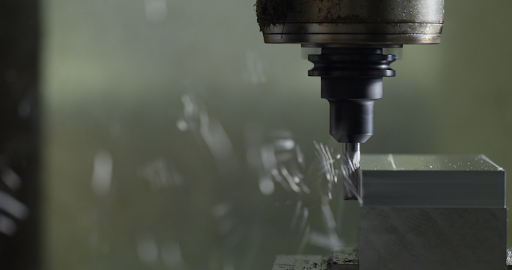
There are several things to specify when choosing to have a component CNC machined such as: material selection, tolerance requirements, geometric constraints, post-processing operations and quality inspection guidelines. Arguably, material selection is one of the most difficult constraints to define, both because of the complicated nature of the interaction with metals and the environment, their response to loads applied on them, and the extensive array of excellent material choices engineers are offered to choose from. Therefore, CNC material selection can be overwhelming. While metal CNC projects may be more common, this material will discuss the most common CNC materials, including plastic CNC materials.
Below is an example of steps to follow in the material selection process for your next CNC machining project:
- Determine what the requirements are for the material’s end use:
- Environmental conditions
- Thermal exposure/heat dissipation
- Conductivity or magnetic requirements
- Mechanical loading requirements (strength)
- Surface finish requirements
- Aesthetics
- Cost or budget
- Weight
- Manufacturing method desired for given geometry
- Identify a potential list of materials, based off constraints above and weigh the following, based off design constraints such as budget:
- Cost vs weight
- Strength vs weight
- Lead time vs cost
- Availability vs manufacturing method
- Make your material selection based off of the most important material requirements and design constraints. For weighing
To get started with selecting the appropriate material for your particular product design, consider the infographics in each section depicting which provides a rough comparison based off of machinability, environmental resistance, and tensile strength: density
information based off alloys available to be machined by Fiction’s Manufacturing Partners at the time of this article’s publication
Option One: Stainless Steel
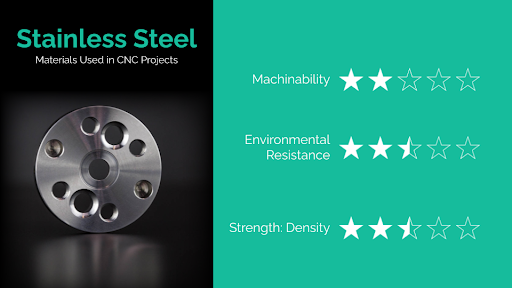
There are many alloys of stainless steel available on the market today. Popular grades for CNC machining are 304, 316, 416, and 17-4 PH. Stainless steels are strong materials that are have a naturally occurring, protective oxide layer, making them suitable for harsh environments. Stainless steel grades vary due to the alloying elements that comprise them. For example, the addition of molybdenum in 316 stainless steel increases its corrosion resistance. Sulphur in 303 stainless steel improves its machinability.
Stainless steel alloys are utilized for a wide range of components, such as consumer products, industrial applications, heavy machinery, surgical equipment, kitchen ware/appliances, aerospace, military and automotive. Stainless steel is also commonly utilized for components which require exceptional strength and reliability, such as shafts, gears, bolts, nuts and fittings.
Stainless steels are machinable, with some grades easier to machine than others. CNC machining of stainless steel is a widely practiced process so most machine shops have extensive experience with the required equipment settings for successful, high-quality machining of stainless steel.
Option Two: Aluminum
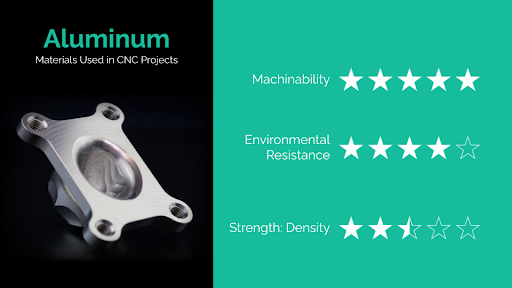
You have probably heard about the utilization of aluminum in a variety of new industries over the last few years, such as for the lightweight frame of a pickup truck or rocket components. Aluminum is an excellent choice for CNC machined components because it is superiorly machinable, lightweight, strong and heavily corrosion resistant. In addition, aluminum alloys are relatively thermally and electrically conductive, making them fit for applications in thermal management and electronics. When determining which is a better fit for CNC machining: stainless steel vs aluminum, cost of materials should be weight, along with the application. Choose aluminum when weight is more critical as it is more lightweight.
Aluminum alloys are commonly utilized in the aerospace, automotive, cookware, medical and consumer product industries. Aluminum is a popular material for casting or brazing. The downside to utilization of aluminum is that it is not always weldable. Aluminum CNC projects may also involve some post-processing or finishing after machining.
Option Three: Titanium
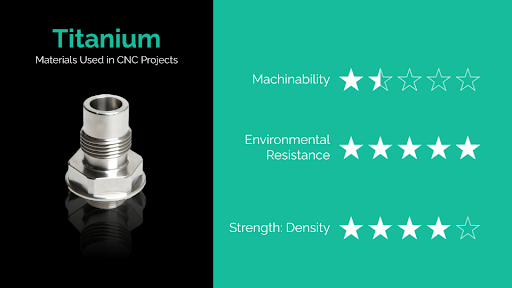
Titanium has revolutionized many industries and provided solutions to some of the most problematic issues in the manufacturing industry. Titanium alloys are tough, strong, relatively lightweight, and corrosion resistant. Titanium is considered to be the most noble metal and be excellent in aggressive environments where other metals may fail.
The medical industry took a full dive into utilizing titanium when it was determined to be biocompatible. Titanium alloys are now commonly utilized for medical equipment and implantable components such as medical screws or devices. These innovative alloys are also utilized extensively in the aerospace, industrial and military sectors for superior strength, creep resistance and their excellent metallurgical structure. For comparison, titanium is about two times as strong as aluminum but only a little over half as dense as aluminum. Titanium is also popular in the consumer product area with products such as lightweight golf clubs.
Option Four: Copper
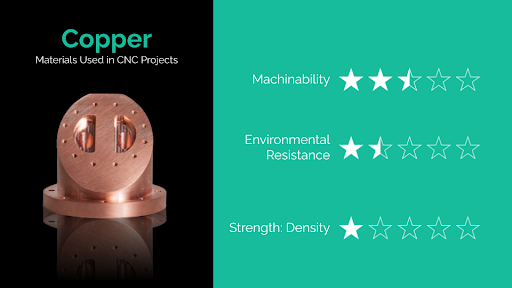
Copper is an excellent electrical and thermal conductor. The only metal that outperforms copper for thermal or electrical applications is silver. Pure (approximately 99% commercially pure) copper is difficult to CNC machine due to its high malleability at colder temperatures and its high ductility. But, a lot of copper alloys exist that are relatively easy to CNC machine and have comparable, if not superior thermal or electrical properties.
Copper alloy 101 is a purer copper alloy. It is good for applications which require high ductility, impact strength, and electrical/thermal conductivity; but it is not good for corrosion resistance. Utilizations for Copper 101 are electronic components, wiring, and electrical components like busbars. Copper alloy 110 is slightly less pure and offers the highest level of electrical/thermal conductivity for any copper alloy. It is also more corrosion resistant. Applications of Copper 110 include superconductor magnets, gaskets, electrical components, jewelry, marine hardware, building materials, and vacuum equipment.
Option Five: Brass
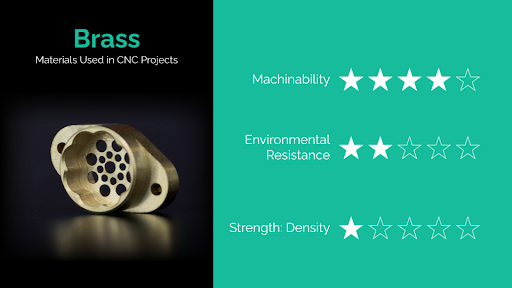
Brass possesses some of the same properties as copper, as it is an alloy of copper and zinc. Brass is durable and easily machinable. This alloy is also corrosion resistant, electrically conductive and it offers a low coefficient of friction. Brass is versatile and suitable for a variety of applications, including plumbing, electrical, artistic, and medical.
360 Brass is the brass alloy with the highest machinability, so much so that it is commonly referred to as free-machining brass. It provides excellent corrosion resistance and strength. The optimal applications for this heavy, strong material are screw machine parts, heavy industrial components, consumer products, musical instruments, electrical components, and plumbing fittings.
Options Six and Seven: Alloy Steel and Carbon Steel
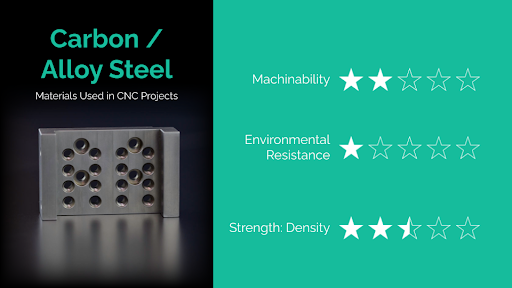
Low carbon steel is one of the most affordable, commonly used steel alloys. As its name implies, carbon steels are comprised of carbon as an alloying element, second in percentage composition to iron. A low carbon steel has a lower carbon content (0.05-0.25%) and is more ductile and weldable but, it is not simply heat treatable to improve hardness as high carbon steels are. Low carbon steels are relatively easy to CNC machine. Alloys such as 1018 steel are used for motor shafts, pump shafts, pins, sprockets, spindles, fixtures, mounting plates, and even hobby components. Alternatively, medium carbon steel is strong and can be induction hardened. Alloys such as AISI 1045 medium carbon steel are suitable for heavy duty applications such as bolts, studs, and shafts.
Alloy steel does not contain carbon as its main alloying element, along with iron. Alloy steel is more corrosion resistant, weldable, heat resistant, and ductile than carbon steel. But carbon steel is stronger than alloy steel. There is low and high alloy steels with the cutoff between the two being either up to eight percent alloying elements or greater than eight percent alloying elements, respectively. Alloy steels are kind of built off of carbon steels, with the addition of one of about 20 alloying elements. For example, low alloy steel 4130 is an alloy with the addition of molybdenum and chromium to improve its hardenability and wear resistance. 4140 alloy steel is an alloy containing chromium, molybdenum and manganese, which increases its strength at high temperatures, torsional strength, and wear resistance. Alloy steels are commonly utilized in industrial applications as well as appliances, silverware, cooking utensils, and automobiles.
Option Eight: Plastics
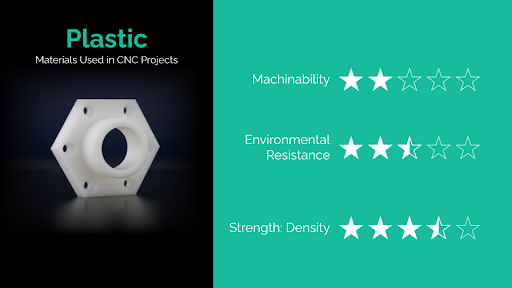
Plastics are an enormous classification of synthetic/semi-synthetic materials that are mainly comprised of polymers. There are many options for an excellent CNC machined plastic component. Some plastics like HDPE are chemically-resistant, electrically insulating, and moisture resistant. Nylon is resistant to friction wear and chemical attack. PEEK is lightweight and resistant to moisture, chemicals, and wear. PEEK can even be utilized as a CNC machining material substitute for most soft metals. Polycarbonate is one of the most commonly utilized plastics in machining; it offers excellent heat and impact resistance.
CNC machined plastics are popular due to their light weight and relatively lower costs. Applications include bearings, chemically resistant containments, laboratory equipment, screws, electrical components and medical devices.
FAQs
- Steel, such as low carbon steel and solid carbide are commonly utilized for CNC tooling.
- Common metals for CNC machining are steel, aluminum, titanium, brass, copper, stainless steel and plastic.
- Softer materials work well with processes like CNC routing or CNC carving. These CNC routable materials include brass, aluminum, acrylic, plexiglass, and wood.
- If you are looking for a CNC machinable material with high tensile strength, look for alloys with tungsten in them.
- If you are looking for a durable metal alloy for CNC machining, look for an alloy with chromium in it.
- 6061-T6 is one of the most popular aluminum alloys for CNC machining.
_____________________________________________________________________
Stay tuned for more in this article series on CNC Materials!Regardless of the material type you choose for your CNC machined components, China Manufacturing parts, Inc. has you covered. Our manufacturing ecosystem provides so much more than just your typical outsourced manufacturing company does. We offer instant online quotes via our intelligent platform which partners you directly with world-class CNC machine shops. All of our manufacturing partners are vetted by our expert supplier quality processes. Our flexible pricing structure allows you to ensure your budget constraints are met while providing you with fast parts that have tight tolerances. In addition, we deliver on high quality by providing services such as hand metrology, laser and CMM inspection. Upload your parts for an instant quote today to see how our innovative manufacturing ecosystem can revolutionize your business.